Its Launched: Sonix IV Technical Support Available 24/7
CHARLESTON, SC November 9, 2009 - Sonix IV Ultrasonics announces the launch of its web based technical support system. The database contains solutions to customer questions and/or issues, and is forever expanding with the knowledge input of Sonix IV personnel and ALL field technicians. Technicians are provided with user information to log-in to the knowledge base to input and share their individual knowledge of specific issues with product users and other service technicians.
In an ongoing effort to become as transparent a company as possible Sonix IV has integrated the company’s Customer Relations Management (CRM) system with the Support branch of the Sonix IV website. A product user or field technician can access the database of solutions by visiting the SIV Support site and simply searching the issue at hand. Sonix IV's public knowledge base gets expanded by capturing informative and helpful knowledge from the community of users. Technicians can share their experiences about field applications and installations, and thus their technical solutions to be utilized by others when the same or similar scenario occurs.
Sonix IV Support on the web utilizes a simple Contact Form to gain further information or access to a specific support tool. The knowledgeable staff responds quickly to submitted information as the integration with the CRM system allows a representative to be available 24/7. The Sonix IV Blog is also available around the clock, and is updated with the most current technical and application information regarding Sonix IV ultrasonics.
Established in 1972, Sonix IV (http://www.sonixiv.com) (http://www.twitter.com/SonixIV) with headquarters in Charleston, South Carolina is a leading manufacturer of ultrasonic cleaning equipment for industry and professionals world-wide. Ultrasonic cleaning technology provides fast, precision cleaning of parts and assemblies commonly found in manufacturing facilities such as automotive, electronics, semi-conductor, and medical devices -professional services such as dental, medical, veterinary, and optical offices - as well as tattoo establishments, jewelry store and repair shops, dive centers and other sporting segments, government, and weapons cleaning for military, police, and enthusiasts.
Wednesday, November 11, 2009
Saturday, October 24, 2009
Sonix IV Tweets for Customer Service
Twitter Users Get Immediate Access to Sonix IV's Customer and Technical Service Departments
CHARLESTON, SC October 24, 2009 - Sonix IV Ultrasonics now offers its customers and field service technicians a unique and easy way to access its customer service and technical service departments using the social networking site Twitter. The company's Customer Relationship Management (CRM) system integrates with Twitter to leverage the power of the social networking site and enhance the level of service Sonix IV provides and improve how the company interacts with its customers, service technicians and prospects.
A Twitter user can simply send their tweet @SonixIV and the CRM system automatically routes the inquiry to Sonix IV's call center notifying the department in real-time of the inquiry and allowing instant interaction with customers, sales representatives, and service technicians. Responses to tweets can be simple comments, or tweets that include url links with detailed information from the Sonix IV knowledge base.
Sonix IV's public knowledge base gets expanded by capturing informative and helpful knowledge from the Twitter community of users. Customers can share their experiences about products, sales representatives can share their recommendations for different types of applications, and service technicians can provide their technical solutions via tweets that can be utilized by others when the same or similar scenario occurs.
Sonix IV President Tom Ray says "integrating Twitter with our CRM program allows us to engage with our customers, sales representatives, and service technicians in real-time and share recommendations and solutions about our products, and our technology. Our goal is to be as transparent a company as possible allowing access to the vast knowledge base our company has compiled over the past thirty-seven years so that our customers, associates, and partners can maximize the benefits our products have to offer."
Established in 1972, Sonix IV (http://www.sonixiv.com) (http://www.twitter.com/SonixIV) with headquarters in Charleston, South Carolina is a leading manufacturer of ultrasonic cleaning equipment for industry and professionals world-wide. Ultrasonic cleaning technology provides fast, precision cleaning of parts and assemblies commonly found in manufacturing facilities such as automotive, electronics, semi-conductor, and medical devices -professional services such as dental, medical, veterinary, and optical offices - as well as tattoo establishments, jewelry store and repair shops, dive centers and other sporting segments, government, and weapons cleaning for military, police, and enthusiasts.
Contact:
Tyler Ray
Sales & Marketing
Sonix IV
phone +1 843-554-0240
Tyler.Ray@SonixIV.com
CHARLESTON, SC October 24, 2009 - Sonix IV Ultrasonics now offers its customers and field service technicians a unique and easy way to access its customer service and technical service departments using the social networking site Twitter. The company's Customer Relationship Management (CRM) system integrates with Twitter to leverage the power of the social networking site and enhance the level of service Sonix IV provides and improve how the company interacts with its customers, service technicians and prospects.
A Twitter user can simply send their tweet @SonixIV and the CRM system automatically routes the inquiry to Sonix IV's call center notifying the department in real-time of the inquiry and allowing instant interaction with customers, sales representatives, and service technicians. Responses to tweets can be simple comments, or tweets that include url links with detailed information from the Sonix IV knowledge base.
Sonix IV's public knowledge base gets expanded by capturing informative and helpful knowledge from the Twitter community of users. Customers can share their experiences about products, sales representatives can share their recommendations for different types of applications, and service technicians can provide their technical solutions via tweets that can be utilized by others when the same or similar scenario occurs.
Sonix IV President Tom Ray says "integrating Twitter with our CRM program allows us to engage with our customers, sales representatives, and service technicians in real-time and share recommendations and solutions about our products, and our technology. Our goal is to be as transparent a company as possible allowing access to the vast knowledge base our company has compiled over the past thirty-seven years so that our customers, associates, and partners can maximize the benefits our products have to offer."
Established in 1972, Sonix IV (http://www.sonixiv.com) (http://www.twitter.com/SonixIV) with headquarters in Charleston, South Carolina is a leading manufacturer of ultrasonic cleaning equipment for industry and professionals world-wide. Ultrasonic cleaning technology provides fast, precision cleaning of parts and assemblies commonly found in manufacturing facilities such as automotive, electronics, semi-conductor, and medical devices -professional services such as dental, medical, veterinary, and optical offices - as well as tattoo establishments, jewelry store and repair shops, dive centers and other sporting segments, government, and weapons cleaning for military, police, and enthusiasts.
Contact:
Tyler Ray
Sales & Marketing
Sonix IV
phone +1 843-554-0240
Tyler.Ray@SonixIV.com
Thursday, August 6, 2009
Tuesday, June 30, 2009
Wednesday, May 20, 2009
Is Your Ultrasonic Cleaner Working, Or Just Making Noise?
The easiest way to check if your ultrasonic cleaner's working up to par is to run the "foil test." A tried and true simple test that can tell you if your ultrasonic cleaner is doing what it should be doing or if it's just making noise.
Using standard aluminum foil, insert a piece that spans approximately two-thirds the length and depth of the ultrasonic bath vertically and hold in place for 30 seconds. After 30 seconds remove the foil piece and examine - there will be impressions (dents) in the foil where the micro-jets of solution have blasted into. The pattern should be consistent throughout the immersed section of foil - if there are any areas that appear unaffected larger than 1/4 square inch (6.35 square mm) then the unit would have failed the test and service may be necessary.
The intent of the foil test is to take an imprint of the action within the bath - not to see if holes will develop in the foil and is why the quick 30 second immersion test is used. If the foil is left in the bath for longer periods of time the ultrasonic action will certainly erode holes in the sample piece - first at the stress points or creases which are the weakest areas then throughout the foil sample depending upon the performance of the unit. Again, this is not the concept - an image of uniform cavitation throughout the bath is what you are looking to capture.
Don't trust the noise factor, do your own "foil test" on a regular basis to make sure your ultrasonic cleaner is up to par.
Using standard aluminum foil, insert a piece that spans approximately two-thirds the length and depth of the ultrasonic bath vertically and hold in place for 30 seconds. After 30 seconds remove the foil piece and examine - there will be impressions (dents) in the foil where the micro-jets of solution have blasted into. The pattern should be consistent throughout the immersed section of foil - if there are any areas that appear unaffected larger than 1/4 square inch (6.35 square mm) then the unit would have failed the test and service may be necessary.
The intent of the foil test is to take an imprint of the action within the bath - not to see if holes will develop in the foil and is why the quick 30 second immersion test is used. If the foil is left in the bath for longer periods of time the ultrasonic action will certainly erode holes in the sample piece - first at the stress points or creases which are the weakest areas then throughout the foil sample depending upon the performance of the unit. Again, this is not the concept - an image of uniform cavitation throughout the bath is what you are looking to capture.
Don't trust the noise factor, do your own "foil test" on a regular basis to make sure your ultrasonic cleaner is up to par.
Monday, May 4, 2009
California Dental Association Show Specials
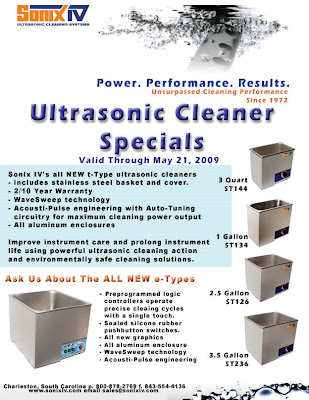
The CDA Meeting starts this week and Sonix IV has just released it's "Show Specials." Our most popular table top units will be on sale through May 21, 2009 - products included in the special are the 3 quart, 4 quart, 10 quart, and 14 quart sizes.
The SS-Series products on sale include stainless steel baskets, stainless steel covers, and of course the Power, Performance, and Reliability that users world-wide have come to trust since 1972.
Saturday, April 11, 2009
Friday, April 10, 2009
Finally, someone makes something...
Finally, someone that makes something! That's the response I got after replying to the typical "what do you do for a living" question from my doctor at a recent visit to his office. Yes sir, there are a few of us left that actually make things in this country, and even fewer of us that haven't opted for the cost savings of sending manufacturing to overseas countries with daily wages less than our hourly wages.
"If you want something done right - do it yourself." We've all heard that saying, but that's what we opt to do at Sonix IV versus following the popular vote of outsourcing our manufacturing to an overseas country. Sure we'd save money, but undoubtedly we'd sacrifice quality. Our technology is a black science that has numerous proprietary nuiances, and when left to human nature where we have no supervision there will certainly be shortcuts, and/or component substitutions .
Sure we can provide contractors with our manufacturing guidelines, but there's no assurances. How many substandard products from foreign manufacturers have made the news recently? For companies that are much larger and that have strict policies with personnel in the foreign companies to oversee the manufacturing guidelines. No thank you! If you're going to make something do it yourself and make it right and make sure that your propriety knowledge is built into every product that leaves your plant.
Just like the users of our products we have equipment in our plant that we count on every day - all day long. We don't put much thought into those products they're just there for us each and every day, and if it does break down all hell breaks lose - production stops and has to be rerouted using other resources. We want users of Sonix IV products to have a product in their company that they don't have to think about - we want them to forget about our products, but remember and trust the Sonix IV name for reliability and durabilty.
Follow the crowd overseas? Following has never been Sonix IV's creed - we're mavericks, pioneers, innovators and proudly manufacture our products in the USA since 1972.
"If you want something done right - do it yourself." We've all heard that saying, but that's what we opt to do at Sonix IV versus following the popular vote of outsourcing our manufacturing to an overseas country. Sure we'd save money, but undoubtedly we'd sacrifice quality. Our technology is a black science that has numerous proprietary nuiances, and when left to human nature where we have no supervision there will certainly be shortcuts, and/or component substitutions .
Sure we can provide contractors with our manufacturing guidelines, but there's no assurances. How many substandard products from foreign manufacturers have made the news recently? For companies that are much larger and that have strict policies with personnel in the foreign companies to oversee the manufacturing guidelines. No thank you! If you're going to make something do it yourself and make it right and make sure that your propriety knowledge is built into every product that leaves your plant.
Just like the users of our products we have equipment in our plant that we count on every day - all day long. We don't put much thought into those products they're just there for us each and every day, and if it does break down all hell breaks lose - production stops and has to be rerouted using other resources. We want users of Sonix IV products to have a product in their company that they don't have to think about - we want them to forget about our products, but remember and trust the Sonix IV name for reliability and durabilty.
Follow the crowd overseas? Following has never been Sonix IV's creed - we're mavericks, pioneers, innovators and proudly manufacture our products in the USA since 1972.
Subscribe to:
Posts (Atom)